2020年春节复工之后,西门子数控(南京)有限公司(SNC)的工厂内出现了一些新变化。普通人或许很难发现其中的不同,但在3个月后,这家工厂因此减少了一条表面贴装生产线,工作效率反而提升了20%。
在工业生产领域,提高用工效率、设备效率一直是企业追求的重要目标,工业4.0、工业互联网等概念因此成为该行业的热门话题。而西门子作为工业4.0联盟组织的重要成员,在数字化工厂建设方面经验颇深。目前在国内,除成都数字化工厂外,南京数字化工厂也已进入最后的建设阶段,投产后,产能将增长两倍多,人员效率至少提升20%,单位面积产出增加40%,产品上市时间缩短近20%,同时柔性制造能力大大增强。
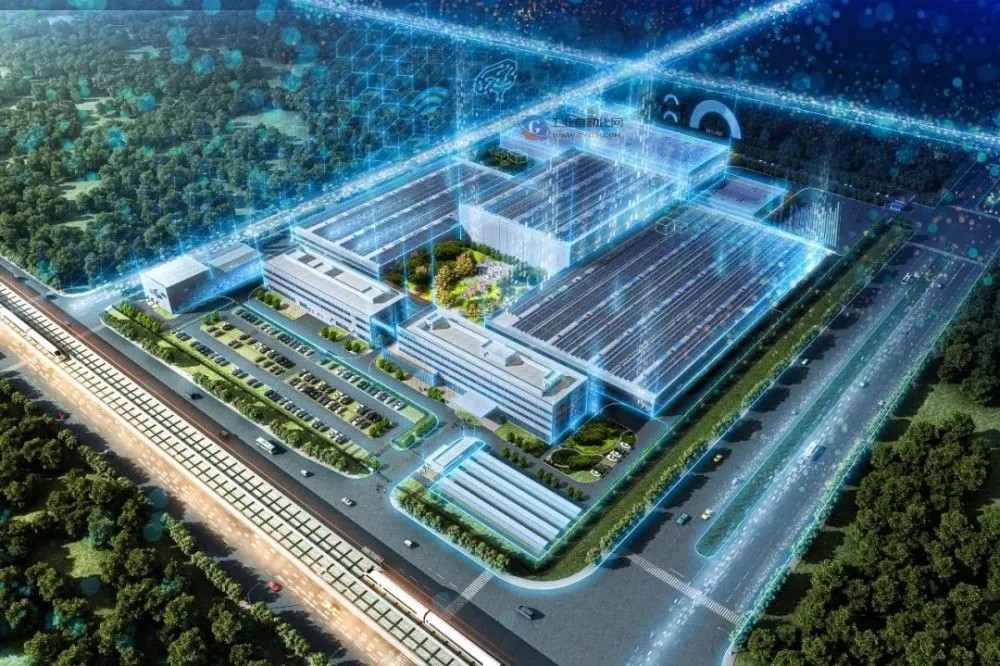
SNC工厂如何通过数字化建设实现这样的制造能力升级?工厂的数字化需要转变哪些管理思维?西门子数字工业业务运动控制事业部制造工厂中国区首席信息官杨泽萍讲述了这段历程。
精益思维,数字化提升生产效能
精益管理思维起源于上世纪80年代末,其核心目标是简单、快速、持续地提高效率、品质,缩短交货期,减少浪费。而随着技术的进步,数字化手段正帮助制造业达成这一目标。
原本,在SNC工厂内有6条电路板表面贴装(SMT)生产线,贴片机本身的自动化程度已经很高,但是否还有提升生产效率的空间?杨泽萍介绍称,SMT生产线是由不同的设备组合而成的,激光刻字、丝印、焊接检测、贴片、回流焊、自动光学检测,不同工序所需的时间并不一致,设备生产厂家不同,往往导致一条生产线上不同设备的利用率并不相同。比如瓶颈工位设备利用率已经达到70%,但仍有设备的利用率只达到40%,那么整条生产线的利用率也会相应降低,需要进行设备或工位的重新配比。
以往解决这一问题,工厂会请工程师人工计算设备的节拍,再通过演算进行配比。但现在,设备本身的操作实时数据通过Valor(MES)制造执行系统汇集在一起,然后根据精益生产的原则和公式,通过仿真程序模拟不同的参数配置进行工艺仿真计算,并通过系统对多条线设备的自动综合排产计划,就可以将生产线调整到最佳状态。“我们这套系统上线时间还不长,性能优化还在第一阶段,不到3个月,我们就减少了一条生产线,而且产量还比原来增加了20%。后续阶段我们还将进一步优化流程,在原材料的管理和质量管理上还有提升的空间。”杨泽萍称。
透明思维,人的经验输入数字大脑
“SNC从十几年前开始,就陆续引进了一些先进的系统,使得我们从比较原始的人工和纸面管理,往计算机控制的系统上发展。”杨泽萍回忆称。而这一过程的本质,是将人的经验变为数据,从而实现经验的透明、可见,以更好地指导管理决策的过程。同时,将产品数字化、研发过程数字化、生产过程数字化,才为数字化双胞胎提供了可能。
以生产线的操作为例,工人完成某一项作业的熟练度就是经验的体现,但实际上每一项作业的时间是有数据标准的。“我们引进了动素测量的机制,把所有的动作拆解,一项作业可能拆解成10个、20个动作,细致到将手移动到目标位置是一个动作,拿到元件之后手举起来是一个动作,旋转工具是一个动作。”杨泽萍介绍到,每个动素在国际标准中都能找到相应的时间标准作为参考,形成了不会受到太多人为干扰的操作时间值的基准,改变了原来人工线上掐表的主观数据,更科学地评判工艺流程的合理性和工人的熟练度。“有意思的是,我们是一个全球化生产企业,英国工厂、德国工厂如果做同一个产品,不同国家的工厂比较的时候,有时会发现为什么你用了20个动作,我有22个动作?然后我们就可以去分析、优化。”当现场管理精细到这种程度,必然需要数字化能力的支撑。
“数字化带来的价值是数据驱动的管理决策,不是一个拍脑袋的想法,或者说仅仅是根据经验的预估。”杨泽萍称,“靠经验去判断,你会有一些感觉,但对于重大的决策和改变,因为没有数据的驱动,决策的准确性风险就会非常大。西门子作为一家有着170多年历史的企业,今天仍然屹立在世界百强前列,企业科学决策、管理能力的与时俱进一直是重中之重。”
如今,数字大脑已成为工厂的核心,正如杨泽萍所说:“现在离开网络,离开各种数字化系统,生产、研发、物流都是寸步难行。”在这种情况下,SNC对数字化的软硬件能力的需求也再次升级,不再单纯锚定供应商的品牌效应和价格,而从产品、技术、服务、灵活性等层面进行综合筛选,为数字大脑的建设打好设备与应用基础。“如果产品本身质量很靠谱,又有一套健壮的监控体系,应用软件又能够非常灵活,这样的产品对我们来讲当然更好。”杨泽萍称,“国内很多企业的产品愿意跟随着客户的需求迅速改变,我觉得是非常好的,我也正在努力把国内一些好的产品和解决方案介绍到总部去。”
数字思维,从设备转型到人的转型
建设数字化工厂的过程中,人们很容易将数字化单纯地理解为设备的自动化和数字进化、决策工具的数字化。颇为热门的“黑灯工厂”理念便是如此,它认为在极致自动化的未来,工厂可以不需要人的参与。但杨泽萍认为,人机结合才是未来发展的大趋势:“柔性的需求越来越多,可自定义的产品的出现会挑战工厂的生产模式。互联网去掉了很多中间环节,从用户的需求到工厂的生产和交付,这条通路会越来越短。世界不停改变,数字化工厂最大的价值不在于把它打造成无人工厂,而是要打造成可以跟上社会和技术变革、更具柔性、更高效、更高质量的工厂。”
人的地位在数字化工厂中依旧重要,在许多企业的数字化转型过程中,面临的棘手问题都是人的问题。不理解数字化的目标与重要性导致数据归集工作无法推进,不具备相应的技术知识储备导致数字化应用无法落地实践等。“数字化过程中面临的问题最难的往往都是人的问题。”杨泽萍称,所以企业需要推动人的数字化意识,让员工养成关注数据、应用数据的习惯与能力。
为此,SNC推出数字化竞争力理念,推动蓝领、白领员工的数字化。在生产现场,通过自动化的商业智能(BI)平台透明的数据展现,细致深入的多方面数据评价维度,原本由各种因素造成的问题被充分暴露出来,生产流程被理顺,工作效率得以提升,蓝领员工的薪资体系也进行了相应的改革。“这样之后你就发现,大家开始更关注数据的来源、逻辑和数据质量了。”
目前,在SNC的业务部门中,IT部门主要的责任是提供和维护数据的平台和技术方案。业务部门譬如财务、采购、生产部门,都是员工自己在应用数字化的工具和技术进行分析。“我们能看到各部门的数据分析的量级和水平在飞速提高。”杨泽萍称,“因为这是各业务部门的舞台,只有自己才知道自己要什么,通过自己对数据的深入分析,才会理解数据的价值。这不仅仅是员工IT技术能力的提高,更主要的是会改变思考问题的方式。”
质的变化正在发生。如今,SNC各部门在招聘人员的时候,基本都会对数字化软件的应用能力加以要求,一些业务部门甚至会要求员工具备一定的编程能力。
那么当全员具备数字化能力的时候,企业的CIO与IT部门又该承担怎样的角色?“我们在内部叫Business Partner(合作伙伴)。”杨泽萍对此早有思考,她认为IT部门需要具备咨询、支撑,甚至驱动业务数字化的职能。“IT因为和信息技术的发展最贴近,对于数字化技术的趋势变化也应该是最敏感的。我们IT应该保持足够的好奇心和学习能力,充分了解企业的业务痛点和发展方向,不断尝试新的技术和方案,把好的、适合企业的新技术及时带给大家,告诉业务部门你有哪些选择,让业务部门自己在里面创造价值,成为他们在数字化技术上最可靠的伙伴。”目前,SNC的IT部门就在研究比如Mendix这种低代码应用开发平台,帮助业务部门更好地实现快速增长的业务目标。
2021年,SNC新工厂即将投入使用。在工厂正式落成之前,工程师们就已经利用数字化双胞胎技术,在数字化平台上搭建出了新工厂的业务架构,完成了虚拟生产和调试,预先发现问题并加以解决,再加上近年来SNC全员数字化竞争力的构建,杨泽萍称:“人们越来越深入地理解了这种数字化理念,从研发开始到产品制造、物流运输、产品服务,数字化思维已经深入到了工厂的每一个环节,这时候整个工厂才是一个数字化工厂。”
数字大脑计划的价值体现
生产一线的信息化建设早已有之,而在进一步数字化的过程中,“工业数字大脑”正为SNC带来更多价值:
● 数字化能力的养成协助SNC完成从精益工厂到透明工厂,再到数字工厂的转变,期间不仅提升了生产效能,也让员工养成了以数据解决问题的思路,最终形成业务模式的数字化升级。
● 更智慧的业务决策:SNC以数字化手段指导生产决策,有效实现生产现场的降本增效,节约生产线投入。同时,数字化工具深入各部门,由一线业务人员进行数据分析,辅助业务决策。通过数据分析暴露出来的问题,通过不断更新换代的技术,比如工业5G,物联网、区块链、人工智能、增强现实等,在持续改进的基础上提供了各种技术创新和技术革命的可能。
● 更敏捷的业务部署:应用数字化的自动排产系统,SNC可以敏捷响应生产的相关元素,如原材料供应情况、设备产能、员工数量等,自动而灵活地进行生产排期。
● 更高效的业务运行:在工厂投产前,SNC的工程师已经利用数字化双胞胎的方法,在数字化平台上搭建出了新工厂的业务架构,完成了虚拟生产和调试,预先发现问题并加以解决。这一机制也将在工厂投产后为安全生产提供保障。
● 更安全的业务环境:在社会全数字化的未来,物联网、云技术的广泛应用,工业信息安全将成为制造型和产品型企业的最大挑战之一。这不仅仅是因为工业终端产品本身越来越智能化的属性而带来的强制要求,其制造过程的信息安全,也成为了数字化工厂的第一目标。西门子通过自己的工业安全产品和信息安全体系建设,在这方面已经走到了行业的前列。
在解决数字化转型中遇到的问题时,一是需要建立开放的企业文化,鼓励大家提出问题,通过开放的沟通解决利益相关问题;第二要允许犯错,创新是要付出代价的;第三就是管理层要有清晰的愿景、坚定的态度,这样才能避免执行层面的观望和徘徊,形成统一的认识。
数据是新时代的原材料,数字化终将改变企业的生产模式、业务模式,也改变了人对整个生产过程的理解。